MEKE3コラム
2020.03.19
前処理剤の開発スタート
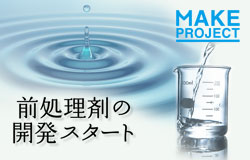
まず、何を作るかを考えてみた。
・綿濃色用
・ポリエステル濃色用
・ポリエステル淡色用
・剥離防止用
・撥水生地用
・メッシュ生地(ビブスなど)濃色用
その他にも、色々あったが、それは後ほど投稿するとして、当時、綿濃色用とポリエステル淡色用の前処理剤は販売されていたので、それで試験を行った。
ポリエステル淡色については、希釈率、塗布量、塗布方法による差が見られず、安定していたが、綿淡色の色相に比べて濃度が薄く、インクの実力が十分に表現できていないと感じた。そこに着目して開発を進めることにした。
綿濃色については、希釈率、塗布量、塗布方法による差があり、加えて、素材の表面品位や組織、プレス条件で大きく変わる事が確認できた。問題点としては、
前処理剤跡、前処理剤変色、洗濯で落ちにくい前処理剤跡、プリント表面のタック、ホワイト表現、インクが浮きすぎた時の剥離、などがあった。
CMYKのインクはカプセル顔料で、内包より、顔料、バインダー、架橋剤の順番でできたカプセル。シロはチタン+バインダーで分散剤などが入ったインクと想定した。
初めに、白インクの上にカラーインクが乗った場合は、相乗性が良いことから、クロTシャツに、前処理剤の代わりにカラーインクのみで出力し、上から濃色モードでシロインク、カラーインクで出力してみた。結果、沈み込んで十分な品位にならなかった。
次に、インクを表面に浮かせてプリントする方向で、撥水剤の濃度条件を変えたもので、前処理し濃色モードで出力してみた。結果、撥水効果に比例して、出力の段階でインクが浮いて流れてしまったり、キレイにプリントできても剥離してしまう。
どうも、出力がカラーインクのみの場合は、カプセルの実力を引き出す為の前処理剤が必要で、シロインクの場合は中途半端に絡めて少し沈み込ませる前処理剤が良いと解った。
先ずは、コンサルタント先の薬品メーカーに、インクと前処理剤の内容解析を依頼してみた。